Reunion Coffee Roasters Case Study: Unplanned Downtime & Poor OEE
How one coffee roaster solved unscheduled downtime and improved OEE by replacing their aging coffee packaging equipment with new VFFS machines.
The coffee industry is evolving rapidly, whether you are a co-packer or a roaster. There are new demands involving customer expectations of flavor and freshness, aesthetics in packaging, residual oxygen levels, and flexibility and formats. Coffee roasters who have traditional equipment have a hard time meeting these demands.
They may struggle with operational efficiencies, fill accuracy, packaging speed, and oxygen levels. In this case study, coffee producers Reunion Coffee Roasters, a well known and highly regarded roaster, is an example of a company who faced challenges with their current equipment and took action.
The leading cause of unscheduled downtime within facilities remains aging equipment - 42%
About Reunion Coffee Roasters
Based out of Oakville, Ontario, Canada, Reunion Coffee Roasters is a leading figure in the coffee industry, as indicated by their Macro Roaster of the Year award in 2015. They have a passion for their product as well as a focus on maintaining a high level of support, quality, and personal relationships with their suppliers as they continue to grow.
Their experience and philosophy has allowed them to be successful and continue to see success in the coffee roasting industry.
The Problem: Downtime and production chaos.
While growth and demand were welcomed, it also triggered a new set of production obstacles involving unscheduled downtime and inefficiency in production.
It was determined that the root of these impediments was aging equipment.
Obstacles with aging equipment:
- Could not handle the current workload
- Unplanned downtime
- Inconsistency in bag formation
- Inaccuracy in fill
- Reduced operational efficiency
These issues motivated an active search for a business partner that could provide them with the equipment they would need for roasted whole bean and ground coffee packaging.
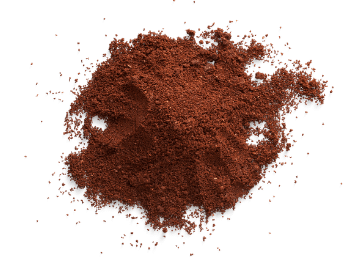
The Selection: Choosing Rovema and Their VFFS
They approached this process with an open mindset toward the vendors who presented VFFS packaging solutions. Greg Rusciolelli, Vice President of Operations, researched options and then attended packaging trade shows as an opportunity to meet with various vendors.
This enabled him to narrow down the field to three manufacturers, all of whom would make a site visit to the Reunion Coffee Roasters facility.
It was at this point that Rovema started to differentiate itself in a few areas, causing Reunion Coffee Roasters to choose them as a vendor.
When looking at components of the machine, they were interested in the following:
- Quality of the finished product
- Quality of the machine
- Run rate
- Price
The bottom line is that many companies make VFFS machines and have technical features that were important to Reunion Coffee Roasters.
Rovema, however, was an organization whose expertise and service they felt comfortable with and whose machine’s unique features would make a difference in their current application.
The VFFS machine types purchased were the BVK and BVC. The BVK was utilized for the production of coffee frac packs. The BVC machine was required for larger gusseted bags with the incorporation of degassing valves.
Both machines demonstrated significant performance boosts over the aged equipment and have helped Reunion Coffee Roasters achieve and exceed the desired solution. With the decision made, they were on their way to implementing a solution that covered their issues of business growth and demand, aging equipment, and reliability.
How Rovema Differentiated Themselves
Engagement with experts: At a trade show, they introduced Rusciolelli to a variety of experts who were able to engage and answer any questions.
Customer testimonials: Reunion was invited to an event where he was able to interact with past and current Rovema customers. Their recommendations provided the positive reviews Rusciolelli needed to feel confident about their decision to partner with Rovema.
Site visit: Rovema was the only company to bring in someone other than the sales manager, again providing expert knowledge when and where it was needed.
Results: How Rovema VFFS Machines Helped
Quality enhancement is an important feature for Reunion Coffee Roasters. With the new machine line, they were able to accomplish this by increasing the output, decreasing the overall cost of ownership, and reducing labor and unscheduled downtime due to maintenance.
At the same time, they were able to improve the quality of their bags. With nitrogen generated on site, Reunion has always been able to have low residual oxygen levels.
However, with the new VFFS machines in play, they were able to bring the oxygen levels down even further, well below their former targets.
There was also more consistency in the forming of the bags and stricter controls when it came to accuracy, weights, and rejects.
Immediate gains achieved for each machine are:
-
- Capacity increase by a factor of >2 (based on run rate)
- Decrease in residual oxygen levels to maintain 2%
- 30% OEE increase
-
- Capacity increase by a factor of 3 (based on run rate)
- 20% OEE increase
- Consistent and improved forming capabilities have enhanced aesthetics of the gusseted stand up pouch
- Scale measurement accuracy eliminated the need for a manual QC process
- Decrease in residual oxygen levels to maintain 2%
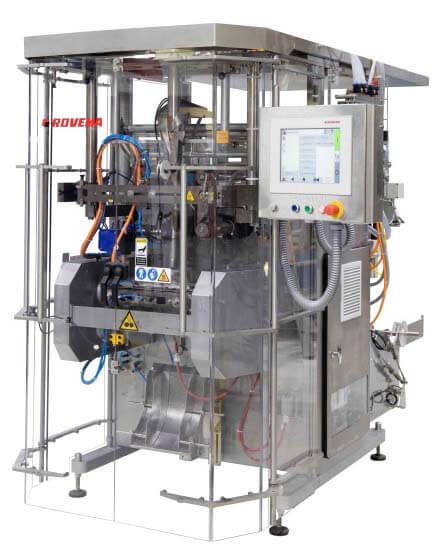
In addition to current immediate gains, both machines are expected to see additional increases in OEE gains of 15% or more. This is because the equipment helped identify and improve areas in their process related to material availability, inline quality controls, and changeover logistics.
The reliability of the machines has also enabled a more accurate production forecast. From an operator standpoint, Rusciolelli states that “the machine operators are highly engaged and enthusiastic with the changes.”
Are you a coffee roaster that needs your high-quality product packed in a high-quality bag?
Reunion Coffee Roasters recognized a need to replace their traditional equipment and turned to Rovema for solutions.
They improved efficiency, performance, downtime, and quality. We'd welcome the opportunity to do the same for you.
“Good employees that are easily accessible. Solid equipment.” - John B.