Webinar: 5 W's of Preventative Maintenance for your VFFS Machine
Who, What, When, Where and Why - The Keys To A Preventative Packaging Equipment Maintenance List For Your VFFS
- A checklist
- A plan
- A process
Sure, PMs are important, but they don't always happen. And they don't have to be a big deal. They can be pretty simple when done consistently.
VFFS experts, Don Lawrence and Shahram Shariff, took us through standard procedures and key requirements - an efficient look at common tips and tricks for cleaning, checking, and replacing various components of your vertical bagger.
We covered topics including:
- Who: What roles play a part in preventative maintenance and maximizing the machine's performance?
- Where: What machine areas must be cleaned and checked for wear?
- What & When: Daily, Weekly, Monthly, and Semi-Annual Preventative Maintenance tasks recommended by VFFS experts.
- Why: Short-term and long-term benefits of consistent preventative maintenance of your Vertical Bagger.
Want to Download The Preventive Maintenance Checklist PDF?
-
Read the Transcript Here!
Webinar Transcript:
Emily Brogan
Well hello everyone. Thanks for tuning into today's webinar on the five W's of preventative maintenance for vertical form fill and seal machines. My name is Emily Brogan I am the marketing and sales coordinator for ROVEMA North America. With me today I have Don Lawrence, our technical parts and warranty specialist for the life cycle services team, as well as Shahram Shariff, our engineering manager who actually oversees and supports our customers and sales teams with the engineering specifications for the new machines. So between the two of them, we actually have over 60 years of industry experience on our call today. So that's exciting. While I give everyone a chance to join us, I want to do something a bit interactive. So I am deploying a poll real quick. And you should have seen it just pop up and it is going to ask you what three outcomes from consistent preventative maintenance on your vertical bagger are most important to you. Also, if you're able to stick around to the end, we're actually going to have a short one question quiz at the end too and our first five correct answers are going to get some swag. So while you're submitting your answers to the poll before I hand it off to Shahram and Don, First, I want to tell you a quick story. So I want to tell you about a plant that bought a new machine. You know, after installation and training, it ran beautifully. It even exceeded their expectations. But after the next year, a couple of shifts supervisors had left for other jobs and the plant brought in some new folks. So then about six months later corporate said, we're looking at a tough quarter, we're challenging you to cut spare parts expense and on hand inventory by 20%. And then a year or so after that the director of maintenance retired and a couple other processes that they used to have in place but maybe not in a formal SOP they became a little neglected. And then a few more things happen after that. And before you knew it three years later, that machine was running at about 70% of its original capacity and what it was designed for. And guess what that story isn't about one specific plant or customer or even exclusive to a vertical form fill and seal machine, you know, this same thing will happen to my car if I don't take care of it. So that's the thing about preventative maintenance over time, a bunch of little changes can have a cumulative huge difference. And that's why we're here today. That's why I'm so excited to have Don and Shahram on this call with me. So they're actually going to show you how to turn this typical history and machine performance, this story that we hear time and time again, in what you ought to expect, which is consistent production over the life of your machine. So now I'm going to hand it off to Shahram, who is going to start going into these five W's.
Shahram Shariff
Thank you, Emily. And as Emily mentioned, my name is Shahram Shariff. I am one of the engineers at ROVEMA, North America. We're here to share with you the importance of preventative maintenance especially those little simple daily ones. What those will get you is five great outcomes. What are these five great outcomes? The number one great outcome would be maintaining your capacity. You remember the reason when you purchased your machine? The reason was that you wanted to get a certain number of bags, good bags, out the door, day in and day out. Over time, for various reasons, and Don will show you what those reasons are, the original capacity would fall. We're here to tell you that based on our experience, and our customers experience, preventative maintenance plays the major role in maintaining the original capacity of your machine. The second great outcome would be part longevity. You purchase your machine based on a certain production capacity. Your production capacity hinges around all parts functioning as they should, day in and day out without a hitch. I'm here to share with you that the secret to parts longevity is to take care of your machine by applying these little preventive maintenance tasks. Also, if you happen to have replaced any one of the original parts, with cheaper parts with less expensive parts, then you are risking parts, premature failures, and you might be in for a surprise here and there without even being able to predict it. The third great outcome would be seal integrity. I'm thinking there's nothing worse than people showing up from the end of line, or getting news from the customers or plant manager or so on that all of a sudden 10s of thousands of bags 10s of thousands or hundreds of thousands of pounds of products have gone to waste. Because the seal integrity was compromised. Everybody is going to be looking over your shoulders to look for answers Why? We're here to tell you that as a component of preventive maintenance, if you had cleaned that vertical seal band, you wouldn't be in this situation that you are today. The fourth great outcome would be downtime avoidance. You didn't buy your machine so you can be repairing and stopping it and working on it every day. Just like seal integrity, or did I miss the seal integrity? Let me go back to Yeah. So just like seal integrity, if components especially crucial ones, that means those that touch your bag, day in and day out, are maintained by preventative maintenance. You avoid premature and unexpected failures. Finally on the list of five great outcomes is the lower scrap rate. Just like sealing integrity, if you have a failure, say compromised seals, with or without even you knowing it, it may be too late, you can lose 10s and hundreds of hundreds of thousands of dollars in a jiffy. We're here to share with you that a few simple tasks as Don will go over and he will share with you will avoid this kind of disastrous outcome. Now, in order to be able to to achieve these outcomes, there are foundations with four pillars that are necessary for you to follow. These are what were who and when of what needs to be done to achieve the five great outcomes we touched the maintaining capacity, spare parts longevity, seal integrity, downtime avoidance and lower scrap rate. So the number one pillar is consistency. daily tasks are the most important for a smooth shift. To be sure, SOP's are the key to consistency and follow up even through turnover challenges. Number two is the team member accountability. You need to arm your operators and maintenance people who are your most valuable assets in your plant and arm them with SOPs geared toward factors specific to your operational environment. The third one on the list of foundations is reliable spare parts and reliable wear parts. Again, if you purchase your components, let's say seal band seal jaws, springs, bearings, on and on, at a lower cost, be prepared to be surprised because not all parts are made equal with longevity in mind. And most of the time, I'm afraid you won't even know that the parts are about to fail. Things are going smoothly and all of a sudden you get a surprise. the fourth pillar of the foundations the maintenance schedule. Now that you've got the follow ups, you've got your SOP, you got your team together, you got your SOP, a checklist ready, operator and maintenance buying, you have to own it, incorporate it into your team's daily routine, and follow up, make sure that it becomes a habit, an integral part of your daily operation. With that, I'm going to hand it over to Emily. And here the specifics of these tasks from Don.
Emily Brogan
Thanks, Shahram, for walking us through the foundations, especially the outcomes that we can expect from them. Now we're actually going to dig a little deeper, we're going to go through some of these imperative tasks, and then towards the end, we'll open it up for some more technically specific questions at At the end, you should see that I dropped the link to the checklist in the chat feature for you to download. I do want to stress that some difficult products or even harsher packing environments could require component maintenance more often. This is not a one size fits all list, you'll likely need to add some additional model specific tasks in the open lines. Don't hesitate to reach out to us if you have any questions on your cleaning intervals. We are more than happy to answer these questions for you. So now Don Lawrence is actually going to walk us through some of those most important tasks on our checklist.
Don Lawrence
Thank you Emily. My name is Don Lawrence and I've been with ROVEMA for 30 plus years. The first 28 years I was with ROVEMA, I was in the field service department and throughout the years and working with many of our other service technicians, many of our engineers Many of our customers, we've noticed quite a few things and we'd like to share some of those with you and the things that we've noticed are your operation, operators and maintenance people are very key people to maintaining your equipment and keeping the equipment running. The operators play a big role in this and they need to take care of a few daily tasks in the first 10 minutes of your shift. And this will increase all of your productivities and longevity of spare parts and just reduce your downtime and your scrap rates. So without anything being wrong with the equipment and the equipment is set up properly, operators should be able to form the perform these daily tasks in the first 10 minutes of their shift. And they should be able to run problem free throughout the rest of the day or the rest of their shift. And we say the first 10 minutes of every shift because we don't know if you're running one shift two shifts or three shifts, this will vary from plant to plant. So, I would like to talk to you about number one, the vertical seal area. This is one of the areas that your operators are going to take care of. But this is a very important area provided the vertical seal bar is set up to strike the tube and the vertical seal in your film squarely and properly. We should be able to open up the Vertical seal bar remove the vertical seal band if you have one, if you have a continuous motion machine you're going to have a vertical seal band, you have an intermittent motion machine, you're just going to have a vertical seal bar. So, cleaning the vertical seal bar on an intermittent motion machine is just exactly that taking a stiff brass brush. We also have to keep in mind that there are two different types of brass brushes one is a long bristle soft brush and the other is a short bristle coarse brush. And the difference between the two are the softer ones should be used on your Teflon coated co bars and the stiff one should be used on a non Teflon coated sealing surfaces. If you have a continuous motion machine, sometimes customers use Teflon coated seal bands. So these have to be treated a little differently. The seal band once you remove it from the machine, it's easy to clean and then you clean the vertical seal bar itself to remove any of your product or film buildup on the bar. These products and film buildup will create a void on the sealing surface where your seal integrity will be diminished. So, clean the vertical seal bar itself, clean the band, put the band back onto the machine, close it and you're ready to go. Next thing I'd like to talk to you about is your horizontal seal bars. Horizontal seal bars are the same. They need to be clean just as much as the vertical bar, they get product build up, film build up and whatnot. Also the horizontal seal bars can be Teflon coated or just normal coating. Teflon coated requires the soft bristle brush non Teflon coated requires the stiff bristle brush, we must keep in mind that the horizontal seal bars are serrated and product tends to build up in the valleys of these serrations. And it tends to get harder as time goes on. So to clean this you must use your brush and sometimes you may have to get some of the tougher particles out by hand. Which means when I say by hand is that we don't want you to use metal tip or putty knife, steel putty knives, screwdrivers or anything like that to clean the serrations if you have to get in there to clear out some of the tougher products, film deposits or whatever, you must use plastic, okay like a plastic putty knife or something like that these steel, putty knives and screwdrivers and pocket knives and stuff like this razor knives, they will take off your coatings in this will just compound your problems. So we don't want to use these on the sealing surfaces.
Emily Brogan
Hey Don, while we're on that note I actually got a question from Tim and he asks, Are brass putty knifes acceptable?
Don Lawrence
Um, yeah, you can use them but we prefer you not dig on the jaws, you know, these will wear the sealant or the protective sealants that are on the jaws. So you want to be very careful with those. Anything metal, we prefer you to use plastic.
Emily Brogan
Okay, thanks.
Shahram Shariff
Yeah, I would I would throw my two cents in there. Also, if you carried out these tasks on a daily basis, you would probably unless you're living in a very harsh environmental conditions, then you wouldn't even be in this situation that you would have to scrape out those particles around the valleys. Is that correct? Don, do you agree?
Don Lawrence
Yes, sir. I agree with that. 100%. if we do this, in the first 10 minutes of every shift, you should never come to the situation to where you would have to dig inside of these. valleys on the serrations. That's why this first 10 minutes of every shift means that you get no more than eight hours or 12 hours depending upon your shift length at a time period between cleanings so you theoretically you should never end up with any of these harsh buildups, like Shahram just mentioned.
Emily Brogan
Okay.
Don Lawrence
Yes, we do recommend that you use a plastic that doesn't melt of course, our jaws, your temperature ranges should be somewhere around 300 to 350 degrees maximum with the majority of films that are used on these machines. Okay, so the next thing we'd like to talk about is the front seal bar with the knife Your front seal bar on all of the later machines. The knife resides in the front seal bar. We want to use the same brush that we use to clean the jaws Be it Teflon coated or non Teflon coated. The knife is just pushed out by your thumb and the serrations on the knife blade can be cleaned very easily with these wire brushes, these brass wire brushes. You want to be wearing a glove these knives are very sharp. So you need a protective glove when you're cleaning these knives. Just be very careful with them. They're hot and sharp. So the next thing we want to talk about is your transport belts. And again, this is just happening in the very first 10 minutes of your shift. So they're being cleaned every eight to 12 hours, your belts will get built up with product that rains down from the delivery system above. So this is where we get most of our questions about. How do I control my bag length better? How do I control my registration better, and 90% of the time, these issues are solved just by cleaning these belts. These belts will get slick after so many hours of runtime. If you run for several days without cleaning these belts, they do get slick and this will create bag length issues and/or registration issues. So cleaning these belts, the operator will open the belts up. Don't remove them from the machine. Just open the belt drive system up. Take a clean damp cloth and wipe each belt thoroughly cleaning it and then take a clean dry cloth and wipe each belt thoroughly drying them off. And then close your belts back up and you're ready to start production again. The next thing we'd like to talk about is the vacuum filters. The vacuum filters on I would say 85 to 90% of all machines, they utilize vacuum belts, that's the belts that you just saw with the holes in them. And this is called a vacuum assist system. This vacuum assist system works very well. But it also collects everything in the environment that is raining down from above. dusty products. Whatever you're running the delivery system above the machine is not 100% clean. So the product comes down onto the belts and it gets drawn into the vacuum filter. So this vacuum filter needs to be cleaned and or replaced every eight hours or every shift. So you should clean this thing and it's very simple just open up the door, open up the lid on the top of this vacuum filter system. Take the filter out and you can either blow it out with air if your plant allows you to do that. Or you can take it to a trash receptacle and just gently tap it on the side and everything will come out of it. Place it back in, snap the lid back in place and close up your doors. The next thing we're going to talk about is the film carriage on the backside of the machine. We'd need to have the operators clean each one of the rollers with a dry, clean rag. And while they're doing this, they're also going to notice whether or not the roller is worn back or stuck. If your rollers are stuck and frozen in place, then they're not turning and they're not allowing the film to move freely through the film carriage. And this will also make the belts out front work twice as hard. So, while the operators are wiping each one of these rollers down, they are also noticing these other defects in them. And it also keeps the product that rains down from above, off of the rollers and off of your film. Okay, so the next thing we're going to talk about is the power unwind belt. The power unwind belt is the drive unit, that drives, assists the roll in motion the roll of film, some of these roles of film get very heavy, and it takes quite a bit to get them in motion. So we put a power unwind back there to assist these film rolls to move. This belt needs to be cleaned just like the transport belts out front. They all three of these belts move the same amount of film and the build up and everything gets on this belt also. So this belt is slipping. It's making your belt out front work twice as hard. So we need to clean this belt again with a clean damp rag, wiping it down thoroughly. And then take a clean dry rag and dry it off thoroughly. Okay, so the next thing we're going to talk about is the air separator. This is kind of important. You have the regulator and the separator. And but you see the smaller device in the front that's where we do our lockout tagout for the air, but the one with the gauge on it. Below it has a canister with sight glasses on it so that you can see inside of it to see if there's water or oil or other contaminants. Just below that, on the bottom there is a thumb wheel or a thumb screw. You can loosen this thumb screw up and drain this thing into a bucket or some type of a receptacle and once it's drained and the bowl is empty. You see nothing in the sight glass and you just tighten the screw back up and you're ready to run again. So the next thing we're going to talk about is the monthly and our I'm sorry, the weekly and the monthly tasks that need to be done. Before we go into the weekly and monthly tasks, I just want to say something about the daily tasks. These are very important. If we do this 10 minutes at the beginning of every shift and your operators perform this correctly, this is going to keep you in production your entire shift. It's going to maximize your output, decrease your scrap rates. And it's also going to help with the longevity of spare parts, increasing the lifespan level. So the daily tasks, take care of 90% of all issues that arise during your shift with just doing this first 10 minutes of every shift. I just can't say enough about that. Okay, so the weekly tasks that we're going to be talking about are your forming collars and your forming tubes and changing out the Teflon tape. On the very center of your forming tube with your belts in the open position in your film moved out of the way, you're going to see on each side of your forming tube where the belts make contact with the film, there are two Teflon strips. We do have some customers out there that have special coatings on their forming colors and their tubes to where they don't use the Teflon strips. The Teflon tape on most tubes resides just underneath the transport belts. These need to be visually checked and probably changed for wears tears. If it's starting to roll, if the adhesive has come loose. product is built up on it or whatever, you can easily just strip this tape off and replace it. On your vertical seal area. You have two pieces there. One is the Teflon tape over top. And then underneath of your Teflon tape, you have a vertical seal strip, we need to check this vertical seal strip once a week to make sure that there are no waves or voids in it. No wear patterns on it. Anytime you have a wavy area, you're going to leave voids in your vertical seal. So this is going to decrease the integrity of that vertical seal. So we need to make sure that that strip is in good working condition. Also to make sure that your vertical seal bar is striking this strip squarely when it's engaged To your film to get a proper seal Once the strip has been inspected and or replaced, then you put your Teflon tape back over top of it and you can thread your tube back up. before you move on. We want you to check the alignment of the last roller on the three setup rollers. To the tube or the forming collar. You can see the three little smiley faces Well, there's only one smiley face and two frowny faces. The last set of rollers three rollers before the film enters into the forming collar. On the backside of your form and collar you have an angle and we want this last roller to be aligned to the point to where you're film lays perfectly flat on the angle of the rear of the forming collar. And you can see on the top one that the last roller is higher than the angle is and the film is not resting on it. This is going to create excessive wear on your forming collar. Because it's pulling on the film and putting undue stress on your film. You may even see little squiggly marks we call them stress marks on your bag. So you want to make sure that it is not riding above. On the second little frowny face. You can see that the film is breaking down to reach the last roller and that also creates excessive wear on the back edge of the collar. This thing will become razor sharp back there if you're if you run it like this for too long. The very bottom one, you see that the film is coming straight off of the angle, right to the last roller. And he's happy. Now with that, that puts equal amount of pressure on your wings of your collar. And it assists with your film tracking from side to side. If you've got this film broken down, the film's gonna want to track funny if you've got it lifted up and fell more track funny also, but it'll also put little lines on your bag, the stress marks that I was talking about. So for equal wear and good longevity of your forming collar, you will want to run it just like the third image on the bottom where the guy's smiling. Okay, the next thing that we're going to talk about is your lubrication. This happens every month. This is on the newer machines, the older machines we used oil to lubricate everything on the your drive systems, your transport systems, your transport belts, everything was oiled. And this was back in the old days, new or newer equipment requires grease. So on the old machines, you would see when you opened up your side door to do this lubrication, you would see actually a tank inside and that tank was filled with oil, and it had a handle on the side of it. And that requires three pumps for every eight hours of runtime to wear the new machines. We have the zerk fittings, and the zerk fittings go to each and every component that needs to be lubricated. The grease lasts much, much longer. So this is why you only do it every month and the oil bath system, you have to do it every eight hours of runtime. So this lubrication system is in the grease is much better. So if there are any questions about these zerk fittings and where they go, what they're lubricating, and the types of grease that you should be using, these can all all of these charts and information can be found in the back of your operator's manual. It gives you the frequency the types of oil, or I'm sorry, the types of grease that you could be using and it also gives you cross references on different types of grease, which they're all food great. If you can't find these, feel free to call us at any time and we can send them to you or two where to locate them? Whatever you need.
Emily Brogan
Those are in regards to the manuals, right?
Don Lawrence
Yes. Yes, ma'am. Okay, did you the entire manual, or we can just send you the charts. We can send you whatever you want.
Emily Brogan
Now, forgive me if I'm wrong in preparation. Don, you mentioned that typically, isn't it three pumps at the beginning of every shift for this type of fitting?
Don Lawrence
No, that's for the oil system. The oil system has a tank inside and that tank has a handle with a black knob on it. And you have to pump the oil three times for every eight hours of runtime. But on the grease system, which is what is all on our newer systems. Geez, I can't even tell you what year we started doing this, but it's been a while. The grease system is it the grease just lasts much longer. Okay. Okay. So if you need any assistance with the lubrications MSDS sheets on the grease that is in the machines or anything like that, feel free to contact us at any time and we can send it to you. Okay, so the next, keep moving here. The next thing we're going to talk about are your safety switches. These are very important devices on your machine and they protect the operators and the people that use the machines and they also protect the equipment. Okay, anytime you open up or break the circuit on any of these circuit, these safety switches, it should act just like striking the emergency stop button. Okay, and these need to be inspected at least every month to make sure that they are functioning properly. This is a very important safety is huge. I know it isn't all of your plants. Most of your plants probably have your own safety guidelines, when to test and when they need to test or replace. So it's very important to keep these safety devices operational. Okay, we just can't stress that one enough. Okay, the next thing we're going to talk about is the cabinet housing filter. This is the same door that you opened up to do your lubrications and it's also where all of the moving parts of the machine are for your film, drive your jaw drive, all of your servo motors, gearboxes, bushings, bearing, shafts, everything are inside of this cabinet. Okay, this cabinet door has a filter in it because we have a lot of heat generating devices inside of the machine. So the inside and all of these devices they need to breathe. Now, these doors are sealed to keep all of the external contaminants from getting inside. So we need to make sure that this filter is clean so that we can get clean, fresh air inside this cabinet with no contaminants from the outside. So once a month, we ask that you open this door up, remove this air filter, clean it and or replace it. Okay? Again, this is just like the other filter it can be blown off or it can just be dusted into a trash receptacle. Okay, next thing we're going to move to is how your daily tasks are completed. These daily casts once again, we just can't convey to you You guys how important these, this first 10 minutes of the shift can make such a difference on all of your, you know, all of the things that Shahram talked about the longevity, the downtime, spare parts, savings and all of this, you can see how this all kind of comes together. And these daily practices are basically on your operators. A clean machine is a happy machine, and a happy machine is a productive machine. So, keeping all of these daily tasks up to date every day. You can see where this can be just a huge cost savings to you and to your customers.
Shahram Shariff
And it's stress free!
Don Lawrence
Stress free,yes.
Emily Brogan
A clean machine is a happy machine. Don, if you had $1 for every time you had to say that to someone, how many dollars would you have?
Don Lawrence
I'd be a rich man. It's also very true. And I've, I've said it for years, and you can't say it enough. And I go into a plant and you see a machine that is just absolutely covered and product. And those are the machines that you're going to be expecting to have problems with. When you go into a plant where the machineis just, it looks. It's 10 years old, but it looks 10 days old. Those are the machines that will last forever. It's just true.
Emily Brogan
Well, thanks for going into so much detail on how we properly conduct all those tasks. Some people are actually already sending in some excellent questions into the q&a section in the chat before we knock those out. Before we jump into that, I want to test how well everyone is listening. So if you don't mind, go ahead and pull up your chat feature if you haven't already. And I'll give everyone a couple seconds to get that pulled up. The first five people to give me a 100% correct answer on this question are going to get a prize, and it's going to be an RTIC insulated travel mug. I don't know if everyone is familiar with the brand. So, I'm stalling just to make sure everyone can get it pulled up. So here's our question. So what were two of the foundations that we covered for achieving outcomes like downtime, avoidance and seal integrity?
Don Lawrence
I'm sorry,
Emily Brogan
That was fast!
Emily Brogan
I think that covers all our winners. So we won't miss any it won't waste any more time. We're gonna go ahead and open up the floor to you guys and have Shahram and Don answer some of these questions, you're welcome to add them in the chat or use the q&a feature. I will mention that if you send it into us anonymously and we don't have time, I know we're already a little bit over our planned time block. If you answer if you send us a question anonymously then then we won't necessarily be able to know who to send a response to later because we are going to go ahead and try to knock these out after our call and get back to you on a personal basis. So let me pull up one of our questions. Here's a good one. What is the stiffness you recommend for the cleaning without Teflon bars.
Shahram Shariff
Without well if you are using a brass brush as Don was suggesting and as we recommend, then the stiffness of it will not play a role in that because you have that is the material is the material that counts.
Emily Brogan
Okay, so it's not as much the stiffness as the material.
Shahram Shariff
Right?
Emily Brogan
Okay. Good to know.
Don Lawrence
I refer to them as stiff and soft because that's just the way they feel in your hand but knowing the exact I don't know that.
Shahram Shariff
Right, Yeah. But as you said, Don, we don't want to scrape those off with this steel brush. Steel brush is much harder and or stiffer but definitely much harder. Whereas brass is Soft.
Emily Brogan
Yes.
Don Lawrence
Yeah. And the steel has is has more of a porous surface on it, which tends to scratch instead of actually brush, you know. Right.
Emily Brogan
So I have one more question that's in regards to the brush and I have: "Does brass, does the brass brush generate any safety issues?
Don Lawrence
No. No more than any.
Emily Brogan
Okay.
Shahram Shariff
No. Again, I want to go back on that and what Don and I talked about that if this is done on a regular daily and consistent basis, then you will not have those buildups on the vertical seal or your jaws to be concerned about really getting into them and digging things out. If you're already if you're already in that condition, then it may be that that cakes up on your sealing surfaces and you may not even be able to remove them whether if you use a putty knife.
Emily Brogan
Yeah.
Don Lawrence
Yes.
Emily Brogan
So here's another question. Which product do you recommend for cleaning the transport belt and the unwinding belt?
Don Lawrence
Which product?
Shahram Shariff
Yeah, I think I think what we recommend is just damp, which means with water clean water is clean water, damp, clean, damp cloth that will do the job.
Emily Brogan
Okay.
Shahram Shariff
So that's the chemical you want to use is water
Emily Brogan
H2O! Okay, I have one more. What are the common problems for belt slippage.
Don Lawrence
The most common problem for belt slippage is like I said in the beginning is the belts are dirty and they have become slick. The tramp the vacuum assist canister is full or bogged clogged. Also if the rollers on your film carriage are not turning freely, if the power unwind belt is dirty and slipping. Now, there are some other issues that could be a possible cause of this and that's your your belts are not aligned to the tube properly you must have good contact Top and bottom, so the belts must be parallel to the tube. You know so that you've got a full complete contact surface. If one side pulls harder than the other, or you know your film tracking goes off, it just creates all kinds of issues. So keeping the belts clean, keeping your film carriage rollers turning freely, and keeping your trans or your power unwind belt clean.
Emily Brogan
Don will alcohol damage the belts?
Don Lawrence
No, as long as it is a denatured alcohol and you can use this on your belts. Denatured alcohol works pretty good really. But it's just not allowed on the production floor in most plants. So we don't recommend that you use it. But it does work very well. In brings the belts back to a nice tacky state. As long as you use denatured alcohol and nothing with hand lotion or anything that will cause the surface of the belt become slippery.
Emily Brogan
Okay. Don, this will be right up your alley. So how often should I preventively change bearings in a vpk. And I know those older models are ones that you're very familiar with.
Don Lawrence
Yes. And the vpk. They're, they're a very good machine and if you're using OEM product, which means you're buying the bearings that we put in the machines from us, and you know, as long as you're buying that quality or that grade of bearing, you should get at least a year out of your crank arm bearings. These are the most common bearings because they're hard to. Some people have a hard time getting them perfectly straight. These bearings are not made to have a side load or anything. But if you get them in there and you get them pretty straight and everything, they should last you at least a year. And so I would count on an annual replacement of these bearings. Now there's a lot of variables in there too. You know? How many the the older...
Shahram Shariff
Are you running, are you running them 24/7?
Don Lawrence
Exactly. Yeah, the variables are if you're running three shifts, 24 hours a day, seven days a week, 365 days a year. You may not get the complete year out of them. Also, if your scale is not set up properly, you know, these old machines, if you're running 120 bags a minute, they these old machines, they start at 120 bags a minute, and they stopped at 120 bags a minute. So if your scale is not being fed properly or it's not running properly, and then the machine starts up and runs 15 bags and stops, and then it starts... waits two cycles and starts running, again, runs 15-20 bags and stops. The start and stop condition is really tough on your bearings. So I will count on a year.
Emily Brogan
Okay. Well, thanks for all the great questions. We are a ways over our time limit. If you took the time to submit a question, I just want you to know that it's not lost in the void again, if it was sent to us anonymously then and you don't feel comfortable resubmitting it with your name, we have, I think, over 200 and something different articles in our knowledge base on our website that discuss all kinds of codes that that your system may throw. So you may be able to do some research there. We're actually going to hop into another meeting just to knock some of these out and we'll respond to you on a personal basis. And for some of these if we need to get our service and support team involved we will just as a parting note, if there's any one specific thing that you guys and gals take with you today is that what you do every day really is your first line of defense against unplanned downtime, product loss, part failure, your MVPs, as Shahram mentioned, are the people that handle these machines every day. These are the core foundational principles and best practices. In our experience and our success with our customers, I want to thank Shahram and Don for joining us today and imparting some of your decades of wisdom on these baggers. And I like to personally thank you, our attendees for listening in on today's webinar. I hope you enjoyed it and we will see you on the next one. Bye, everyone!
Don Lawrence
I hope it all helps guys. Have a good one!
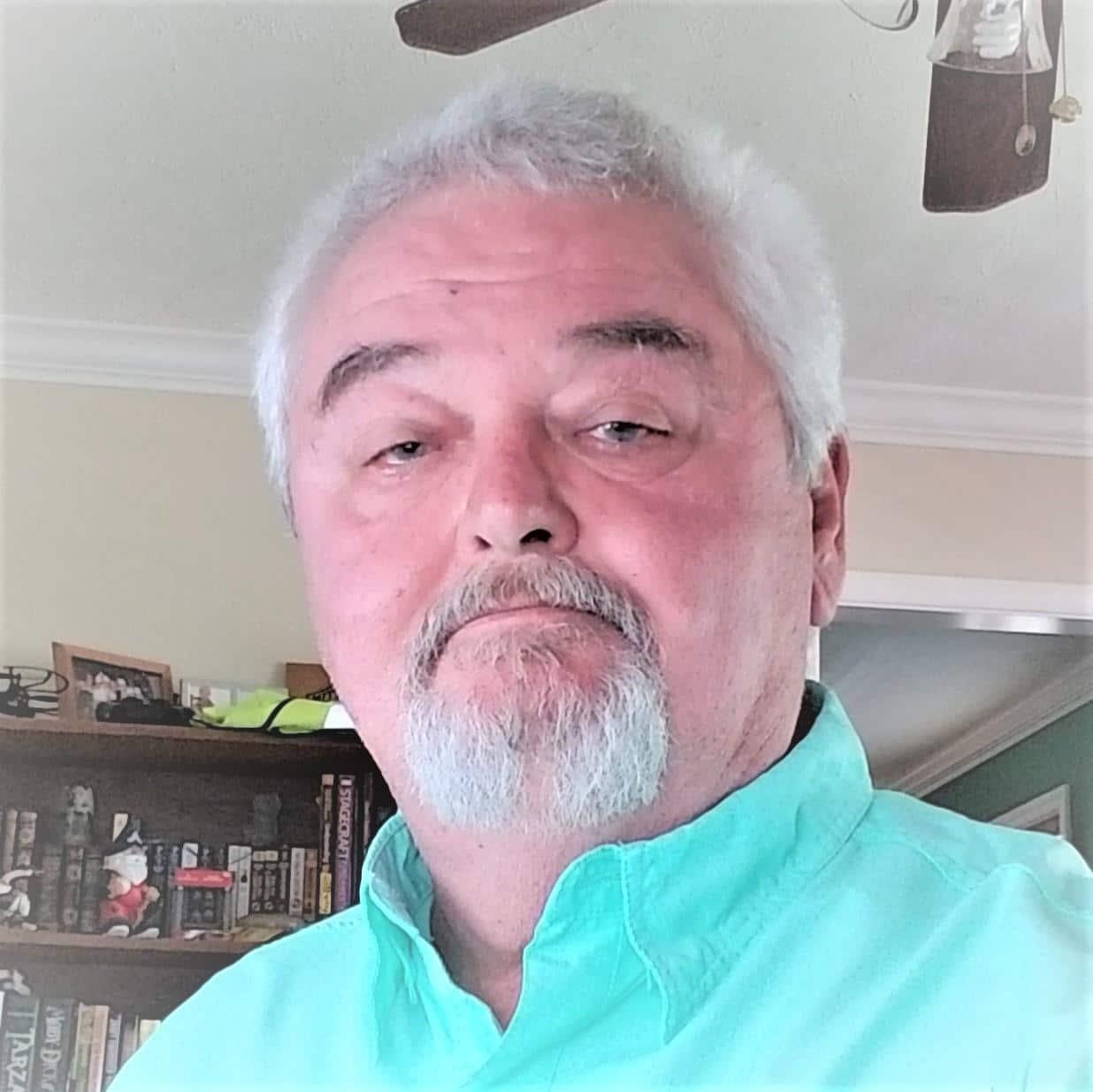
Don Lawrence
Technical Parts & Warranty Specialist for the Life Cycle Services team just celebrated his 30th year with Rovema. He has extensive and invaluable knowledge of Rovema Machines and their plant performance from decades of customer visits as a VFFS service expert.
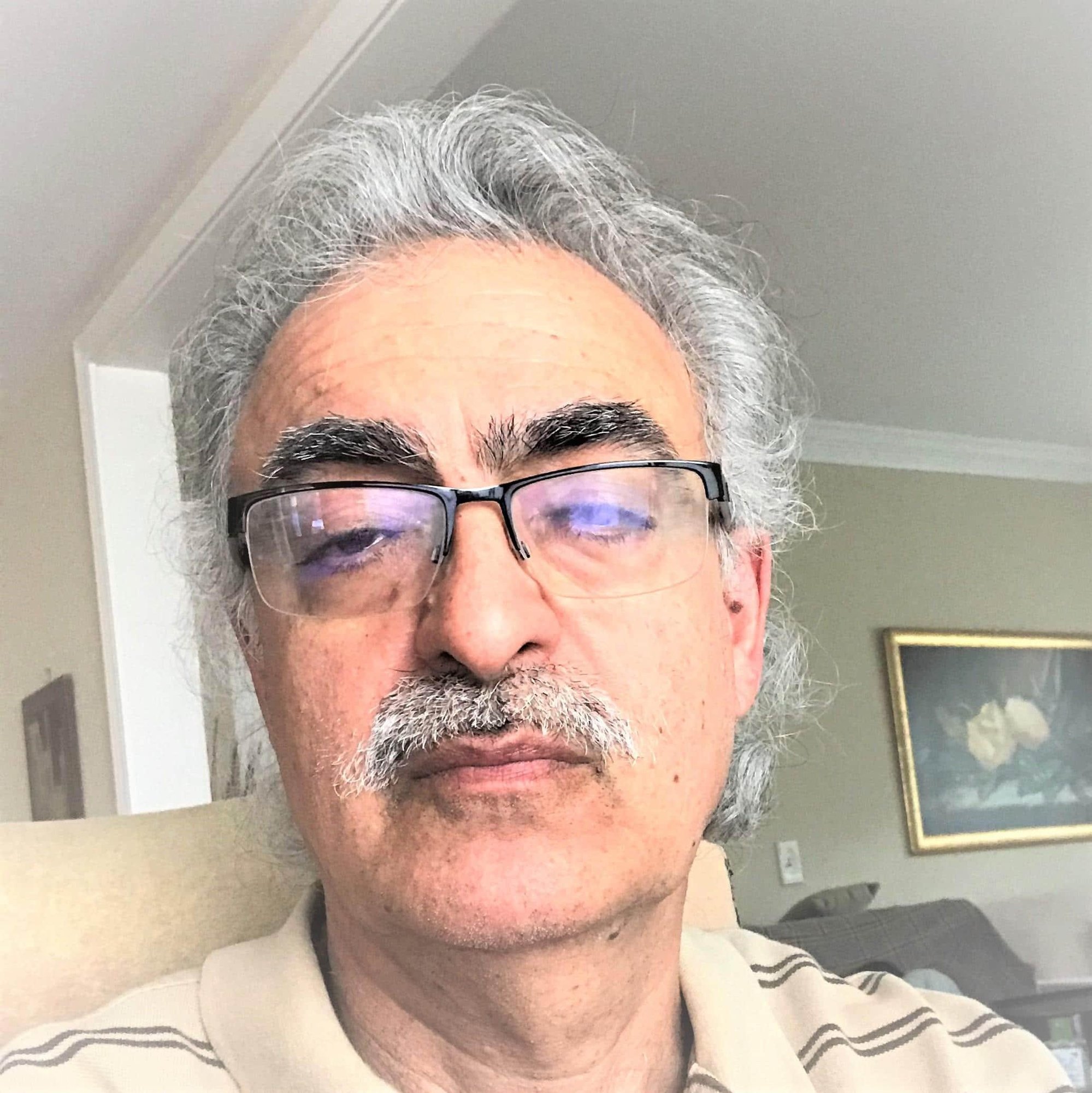
Shahram Shariff
Engineering Manager at Rovema has over 30 years of industry engineering experience, primarily in the foodservice equipment space. With a post-graduate degree in mechanical engineering, he oversees and supports our customers and sales team with the engineering specifications for new machines.
“Good employees that are easily accessible. Solid equipment.” - John B.