ROVEMA Parts, Service, & Support
UPTIME - Maximizing Your Investment in Machinery
When you invest capital in a project you expect the machine to perform as designed. That's a given.
But performance extends well beyond the Factory Acceptance Test.
Can you scale production? Adapt to new requirements? Train new operators?
When your line fails on one of many European holidays, do your customers suffer?
We've built our ongoing support program around a few simple principles:
- If your machine is still running you should still be able to get parts and service, no matter how old it is.
- When you call, we should have a knowledgeable technician available to help.
- Retrofits and VFFS upgrades are a normal part of business - not a distraction.
Incremental Loss of Production in VFFS Machines
We reject the industry mindset that over the years of running your machinery, it's expected that you'll see an incremental loss in efficiency as it ages.
It's our experience that with the foundation of a reliable VFFS machine, proper preventative maintenance, reliable spare parts, and a VFFS service team that is committed to the consistent performance of your machine, your capital equipment will maintain the effectiveness it was built for.
Learn more about how ROVEMA technicians audit machinery onsite for our customers.
Reliable VFFS Machines with No End Of Life
When your VFFS packaging line was built under a single roof in Fernwald, Germany, it wasn't built to last 10, 15, or 20 years, it was built to last a lifetime.
As a part of our no-end-of-life principle, Rovema spare parts for your VFFS machines are never obsolete when you need them.
The only time you should have to shop for a new VFFS machine is when the new technologies are too drastic to be retrofitted to your existing one.
Learn more about Replace vs Rebuild considerations.
Need your Operator's Manual?
We offer downloadable operator manuals which include wiring diagrams & explosion drawings for most machines. (Please note that most machines have custom configurations. If you need specific drawings for your machine, please contact our service department.)
Quick Resources
- Webinar: 5 W's of Preventative Maintenance for Vertical Form Film and Seal Machines
- Blog: "Old Red" Rebuilding vs Replacing your Aging Vertical Bagger
- Tech Note: 5 Tips for Troubleshooting Film Tracking Issues
- E-Book: Maximizing OEE for VFFS Machines
- Blog: Troubleshooting 11 Common Film-Related Issues with VFFS Machines
Visit our resource center for other helpful materials including tech notes, training tips, and general V/F/F/S information.
Training Programs
Get long-term profit from a properly trained team and maximize the efficiency of your machines. Our training programs have a modular structure, allowing us to customize a program based on your solution.
Theory and practice are optimally intertwined, simplifying operation and routine maintenance work on your machine.
Training opportunities are hosted online or at our manufacturing facility in Fernwald, Germany. Alternatively, we will consider having the training on your site, if this is preferred.
Submit a Ticket / Inquiry
Do you need spare parts, or information on training, or are looking to make an upgrade to your ROVEMA equipment? Please use the form to submit a request!
Once submitted, our team will reach out to get you what you need!
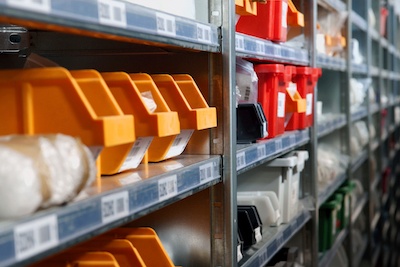
Replacement Parts
If your machine is still running, we'll still have the spare parts you need.
That's our simple commitment.
Occasionally electric/electronic components that we have sourced may become obsolete from the original manufacturer. In that case, we work to develop retrofit solutions.
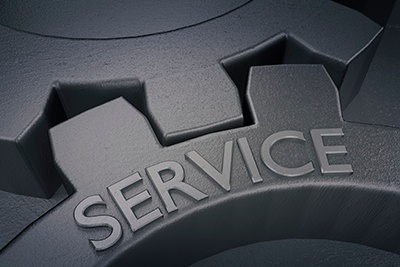
Technical Service
Whether you need field service or telephone support - the point is you need help.
Line design, commissioning, operator & maintenance training, preventative maintenance, and break-fix are all requirements that we support with a staff from our Atlanta office.
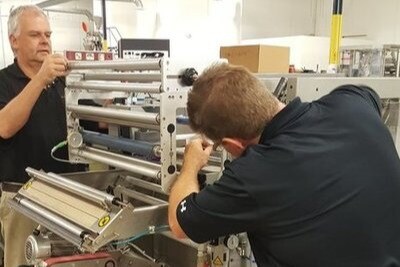
Retrofits, Upgrades, & Rebuilds
Just when everything seemed to be running so smoothly....here comes a wild new requirement!
A key customer requires a new format; an old line is suddenly being asked to outperform. That's life in the demanding world we all face.
Often our team can suggest creative solutions to your requirements.