3 min read
Collect, Buffer, Fill System: Material Handling At the Bagger?
Emily Brogan
:
Fri, Feb 25, 2022
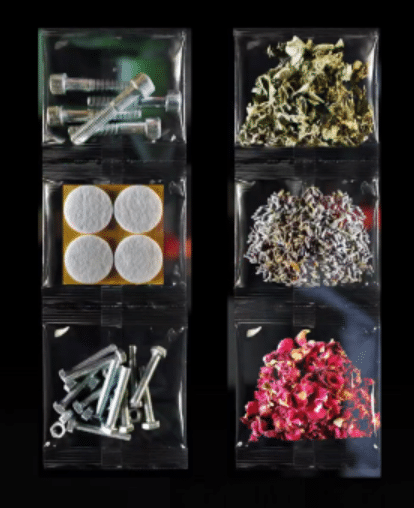
Since the debut of ROVEMA’s new Collect, Buffer, Fill system at PACK Expo in 2021, many questions, product ideas, and scenarios have been brought to the table from producers around the world. If you consider the system’s main capabilities of blending and alternating doses- these are at their core, bulk material handling activities that have been integrated into the packaging equipment as a part of the filling phase.
Of course, it doesn’t integrate many crucial stages that some producers still need like sifting, but the flexibility that this technology is adding to current bagging capabilities could potentially transform daily operations for many industries and product types.
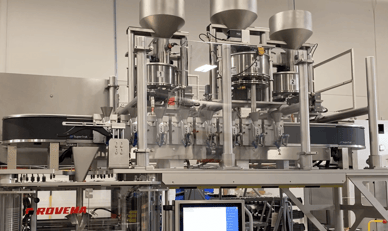
Because of how much flexibility this system can add to packaging operations, it’s easy to see why so many packaging professionals are interested in this new technology. But what factors need to be considered and product types would this be a good fit for?
Quick Synopsis of the Collect, Buffer, Feed System Capabilities
With the Collect-Buffer-Feed system, product doses are collected from several different filling components with electromagnetically driven “shuttles” that travel on a track. The shuttles are then staged or placed into a “buffer” zone of the track above the ROVEMA VFFS machine. The shuttles then feed the VFFS machine and then travel back to the filler to collect another dose.
These systems can handle a wide range of product types, dose sizes, and configurations and are compatible with all traditional fillers typically used with VFFS machines: multihead scales, augers, cup fillers, counters, etc.
Let’s take a look at how the CBF system works and which scenarios this could be a great fit for, and the reasons it might not work for others.
CBF System Capabilities and Ideas
The capabilities of the CBF system compounded with the flexibility of ROVEMA packaging equipment allow producers to accomplish a variety of processes that we've boiled down to a few key categories.
-
Multiple ingredients in a single package at the packaging line
While we wouldn't technically call this "blending" (we will clarify why in a bit), this can be a great fit for anyone looking to get multiple types of product into a single package. For example, if you are bagging salad toppings in small pouches for kits, this could add dried cranberries and roasted pumpkin seeds into one bag together, without having to maintain an even blend of these products.
-
Multifilling different dose sizes, and product types into individual pouches
This could help producers reduce or eliminate work in process or having to outsource multi-packing to a copacker. For example, multiple varieties of flavored almonds could be packed at the same time and sent to a the end of line equipment instead of running each flavor individually, storing them and then case packaging, whether automatically, by hand or by sending finished units to a copacker. This could help producers reduce their capital expenditure if the need for multiple dedicated lines could be eliminated. You could even create a chain of pillow bags with perforations that could be used, like alternating between AM and PM multivitamins or preworkout and postworkout powders.
-
Multiple variety multipacks where each pouch can have different combinations of doses from the fillers
For example, like the salad kit scenario above, instead of packing only bags of cranberries and pumpkin seeds, you could have a dose of cranberries in each bag and alternate between pumpkin and sunflower seeds, if they are needed for different kit flavors.
-
Multiple Package Sizes of the Same Product
ROVEMA's sealing system is powered by direct-linkage servo motors which actually makes having different cutoffs lengths for each package, an existing capability but until now, we have not actually had a customer that needed to be able to use it since filling components are engineered to stay consistent with the same dose size, not the alternative. Using the CBF system would allow you to fill different dose sizes into each package and have differing cutoffs for each.
CBF Caveats to Keep in Mind
With the way that the CBF system operates, there are a few things that are important to understand if you are considering whether this system is right for your operation. The first is the concept of "blending".
The CBF system can hypothetically dose any combination of components, and while you have great control of how much of each component is being added, they likely won't be evenly distributed in the package. Of course, this wouldn't matter for single-use products like meal kit doses of spices, a big bag of trail mix might not deliver on what your customers expect when they reach into the bag for a fistful of product. (Some people might not want a handful of just chocolate, but do we really trust those people?)
What Added Flexibility Could Mean for Producers
From experience, we know machinery flexibility is one of the major characteristics customers cite for evaluating capital equipment. When your equipment can handle more than one type of packaging format or produce different types of bags with minimal changes in setup time and costs, it gives you a competitive edge for today and for the future.
This system increases machine uptime by eliminating the number of changeovers that need to occur when running multiple products on one line and can be a great way for smaller operations to increase their automation, where volumes might not have made automation feasible before.
Want to learn more about flexibility? Take a deeper dive on this topic.
If you're curious about this system and want to bounce ideas off of a technical expert, you can request to book a time with one in the chat 👉👉 or by sending a message to sales@rovema-na.com
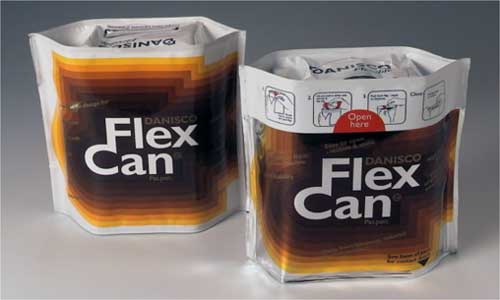
1 min read
Brown Bag Blog Series Pt. 3: What is the Flex Can Stand Up Pouch?
In Case You Missed It: the Rovema Brown Bag Blog Series Over the past few months, we’ve been creating and sharing posts as part of our Brown Bag...
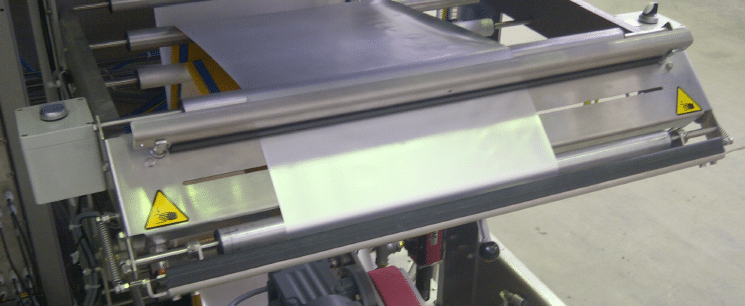
Tools That Improve OEE & Increase Uptime of Your Vertical Bagger

Overall equipment effectiveness (OEE) is a game of inches. With the uptime of machinery having a direct impact on your bottom line, it's always an...