Auditing the Effectiveness of Your Current Packaging Machinery
Have you noticed your packaging equipment slowing down, stopping more often, or wearing through parts faster than it used to?
It’s a common challenge and in most cases, the problem isn’t your ROVEMA machine getting old. It’s the packaging materials or specs that have quietly changed over time. A slightly different film, a few skipped PMs, or even small tweaks in the recipes can throw things off.
The fastest way to get clarity, and your performance back, is with a ROVEMA Equipment Audit. One visit from a certified technician can uncover what’s really going on and give you a plan to fix it fast.
Stop guessing. Start optimizing.
What is an Audit?
As a Life Cycle Services offering, our audits consist of a Rovema Service Technician coming to check your machine from A-Z. Like pre-flighting an aircraft, we start at the nose, go around the sides, look at the top and bottom, and find out exactly why your machine isn’t operating like it used to.
Why should I have an audit performed by a technician instead of letting my maintenance staff do it?
In your day-to-day operations, you probably have multiple team members touching the equipment. Sometimes we hear the operators say things like, “I come in and the settings are all wrong. I know how to run my machine so the first thing I do is change X.”
Chances are that you’ve heard something similar.
When ROVEMA packaging machinery is first installed, each component, and often each recipe is optimized before the technician leaves. Over time, some wear parts might be sourced from different places, or PMs might get skipped, causing some quality or speed issues.
Since ROVEMA baggers are so robust, you can often overcome these results by changing the settings. Therein lies the problem. The settings get changed. Then changed again. Then again.
Do you Need a Second Opinion About Your OEE?
How is an audit performed?
When you’re in the day-to-day operations of your machine, it’s hard to see everything that might be causing the issues. Our Service Technicians are highly trained to spot these issues and bring them to your attention. But what does this look like? (Of course, we can only speak to what our process is.)
-
An audit starts with making a bag…or 50. While the machine is running, our technicians are watching the film move and checking the bags. We are listening for any clunks or clanks that shouldn’t be there.
-
Next, we pull the film off the machine,
-
We look for stray screws or bolts. Often, we will see where someone hasn’t tightened one up properly, and it’s fallen out.
-
We prop up the forming collar and look for Teflon tape on the tube. Sometimes there’s just too much!
-
Next, we square the film carriage. You’d be surprised how daily use and film roll changes can get things out of square.
-
Next, we make sure the vertical seal is centered.
These steps help us get the bagger “back to zero,” meaning that it is aligned as it was initially intended. Once we do this, the problems with the machine start to become clearer. As we perform an inspection of all the mechanical parts, including belts, bushings, bearings, rollers, and clogged filters. We will occasionally run bags for quality checks and build a list of parts that need to be replaced or potential conversions that are recommended. Once we are done, we will clean the rollers and give you some feedback.
What can I expect from an audit?
When a Rovema Service Technician leaves, your machine is going to be back in proper alignment. They will have gone over the findings with you and help you understand the impact of those results. You’ll receive a copy of the report, and then if any quotes are needed for replacement parts or upgrades, we’ll provide that too.
How often should an audit be performed?
There are a lot of variables, so this is a bit difficult to answer. Different factors include how often the machine is run, is the environment clean, is the climate within tolerance, how often preventative maintenance is performed, what the quality of the preventative maintenance is, etc. Generally speaking, we recommend 1 to 2 times per year.
How do I schedule an audit?
Simply fill out the form on the right side of the page, and our Service Coordinator will reach out to you!
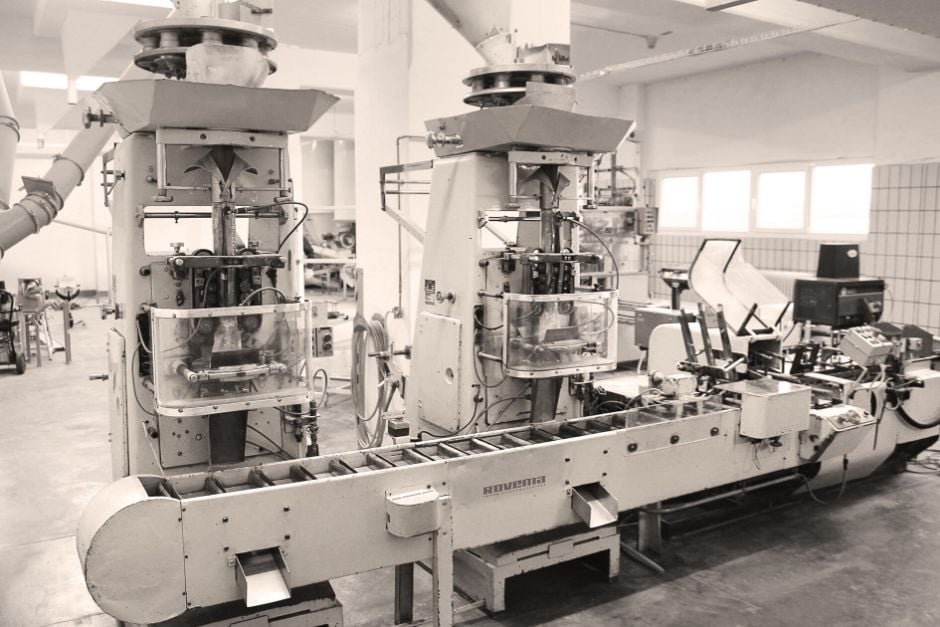