The overall efficiency of any form, fill, seal machinery always hinges on the effectiveness of the sealing process. Packaging has many jobs to do- attract customers, represent your brand, and make you money.
But it's primary job? Protect your product so that it can make it from your factory to the plates of your customers so that it ultimately gets consumed. The seals of a package are often the most vulnerable parts and operators, engineers, and plant managers always have to navigate the delicate balance between output rate and seal jaw dwell time.
Of course, the characteristics of your film material have a big impact on your operation and its overall success as well. Understanding the inside and outside coefficient of friction, sealant layer, and other film specs - as well as discussing them with your packaging machinery supplier is key to knowing and addressing any challenges on the front end, so that you avoid common challenges and have the opportunity to invest in any tools you might need to run challenging film types.
We're going to unpack a couple of the common problems observed while running your continuous motion vertical form fill seal (VFFS) bagger.
Vertical Seal Troubleshooting: Causes and Solutions
1. The vertical seal is open or is weak
-
Problem: The vertical seal temperature is too low
- Solution: Increase the vertical seal temperature
-
Problem: The heating cartridge is defective
- Solution: Replace the Heater cartridge
-
Problem: Temperature probe is defective
- Solution: Replace the temperature probe
-
Problem: The vertical sealing pressure is too low
- Solution: Adjust the air pressure to increase the pressure on the film
-
Problem: Air Cylinder is defective
- Solution: Replace the cylinder
-
Problem: Air solenoid is defective
- Solution: Replace the solenoid
It is also important to check that the vertical seal unit is aligned parallel to the forming tube. If it is not, this will often result in only a portion of the vertical seal being sealed. Refer to the image below for an example of what a non-parallel vertical sealing unit looks like:
Common solutions to a miss-aligned vertical seal unit on a VFFS Machine:
- The overlap of the film may not be correctly positioned under the vertical seal band (Adjust the vertical seal band to correct the misalignment)
- Check that the Teflon tape behind the film on the forming tube is not worn or missing. (If it is, then replace it)
It is also important to check whether the brass insert under the seal band is worn. If it is, it will not transfer the heat correctly. If this is the case for your seal band brass inserts, replacing them will be your best option.
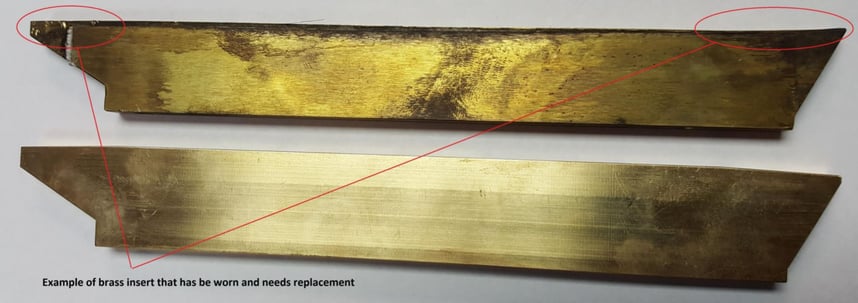
2. The vertical seal band is sticking to the vertical seal or creating wrinkles.
Before diving into the common problems and solutions for vertical seal stinking on wrinkles, we recommend checking first that the film is tracking properly so that the inside sealant layer is not exposed to the seal band.
-
Problem: The vertical seal temperature is too high
- Solution: Decrease the vertical seal temperature
-
Problem: The vertical sealing pressure is too high
- Solution: Adjust the air pressure to decrease the pressure on the film)
-
Problem: Check that the vertical seal unit is aligned parallel to the forming tube.
- Solution: This can cause too much pressure which results in the vertical seal only being sealed at only one spot on the seal
-
Problem: The seal band speed is too slow or too fast.
- Solution: Adjust the speed of the band with the controller
If these suggestions don't seem to be effective, the issue might also be film related. We have another VFFS troubleshooting resource around common film problems that might have the answer you're searching for.
Experience has taught us, over the last 60+ years of supporting customers, that VFFS preventative maintenance is your first line of defense against the common issues that cause unplanned downtime, premature spare part failure, and poor package quality. If you would like a resource to help you build a preventative maintenance schedule for your team, check out our webinar that unpacks all things preventative maintenance, best practices, and even toll recommendations, that you can keep surprises at a minimum.
If you are a current ROVEMA customer (or even if you're aren't!) and these steps don't solve your issue, and you'd like to contact us to talk through your issue over the phone for free or to schedule a service visit, contact our Service Manager by calling 404-640-5322, or you can chat with an expert live in the chat box on the right 👉👉.