Improved Process Using Less Space
Recent PMMI research found that manufacturers in the food industry have aggressive capital investment plans focused on improving process efficiency and packaging. The equipment plans include everything from blending and cooking through primary packaging VFFS lines to end-of-line carton & case solutions. Key goals include "expanding the use of automation, integrating operations for increased throughput and advances in the manufacturing process, as well as better floor space utilization."
While we work with companies in a variety of industries including chemical, pet food and lawn & garden, many of our customers are in the food industry in sectors including coffee, snacks, candy, frozen food and cereal. Our anecdotal experience confirms the PMMI research. We find that companies are focused on increasing speed, improving OEE, and adapting to evolving retail requirements like shelf and retail ready packaging - and that puts the primary VFFS and secondary carton and end of line case packaging functions squarely in the sights of process and packaging engineers charged with these improvements.
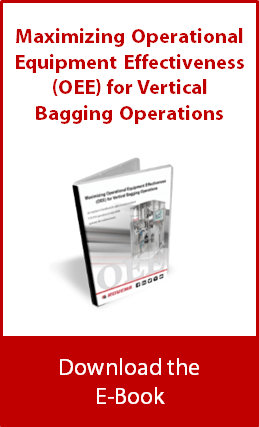
However, when it comes to capital investments, the focus is primarily on equipment rather than facilities. This means that most projects are constrained by space limitations. While process and packaging lines can sometimes be reconfigured, the construction of new factories or the expansion of existing ones is not always possible. Therefore, two-dimensional space planning becomes a crucial aspect of every project. Fortunately, the development of small machine footprints, initially in response to the limited factory space in the EU, has proven to be beneficial for companies in adapting to these constraints.
In addition to the challenges posed by limited floor space, vertical form fill seal (VFFS) applications also face limitations and considerations in the third dimension - height. Meeting the common objectives of increased speed, extended shelf life, and package size/style flexibility becomes challenging when there are existing ceiling height restrictions, often caused by mezzanines. These height constraints can complicate the implementation of continuous motion baggers, as the chassis needs to extend vertically to accommodate the required travel distance of the cross-sealing jaws. This extension is necessary to ensure adequate dwell time for complex film structures at maximum operating speed.
In many cases simply changing from intermittent motion vertical FFS to continuous motion baggers adds more height than can easily be accommodated as the chassis extends vertically to allow for the 9.5" required for travel of the cross-sealing jaws to allow adequate dwell time with complex film structures at maximum operating speed.
The good news is that as clearance becomes a more common constraint our engineers have identified common solutions and have built standard adaptations of our modular machines. We've also created a number of custom solutions. And food manufacturers can control several of the factors that impact line height.
What Determines the Height of a VFFS Machine?
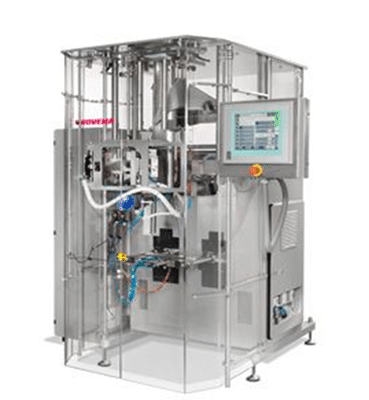
Working from the top down there are a number of mechanical functions which require space. For common food packaging applications these include:
-
feeding - the conveyor bringing product to the machine has to feed the hopper and requires access for maintenance
-
hopper - this typically gets bigger and taller to accommodate the higher speeds of continuous motion applications
-
scales - often more buckets are required to provide required fill accuracy at higher speeds
-
forming shoulder - critically important and often overlooked - the common 60 degree angle of forming shoulders is mistakenly assumed to be a standard. In fact bag width and film structure dictate the angle, and therefore the vertical space required to form the flat web into the packaging tube. Wider webs simply take more space to form, and thicker / stiffer films (e.g. polyester aluminum laminates commonly used to extend shelf life and reduce OTR & MVTR) require more gentle forming (perhaps 27 degree) to avoid fracturing the important barrier structures. This difference in forming angle potentially impacts total machine height by somewhere between 4-8".
-
vertical seal/longitudinal seal - speed requirements and film type impact the longitudinal sealing. Drag sealing and linear sealing require similar lengths - typically 300mm (roughly 12".) Although this doesn't change the total height, it's a factor that must be considered.
-
transport belts - package appearance and consistency are common performance criteria, and controlling the film precisely to deliver correct bag length by eliminating slippage is crucial.
-
bag spreading - bag width comes into play again here. Once the tube has been formed and logitudinally sealed it must be formed again into the desired package shape. There are physical limitations to how acutely this forming can be done in order to control behavior and appearance of the film.
-
cross sealing - the physics of sealing film are controlled by the three well known factors of time, temperature and pressure. Higher speed applications require cross seal jaws which travel vertically to provide the dwell time required to create the expected hermetic seals even in thick and complex films. We know from experience that 240mm (roughly 9.5") allows us to meet extreme requirements. While we can manually reduce the sealing times at high speeds which results in a reduced stroke of the cross sealing jaws, that capability is rarely sacrificed because seal integrity is a fundamental VFFS OEE and performance criteria.
-
discharge chute/vibrator box - Not only must this allow a competed package (longest planned bag) to hang freely, it must also accommodate the space required for the devices required to jog the bag and product to accelerate settling and reduce bag height.
-
take away conveyor - those precious, perfect final bags have to be conveyed back up to secondary packaging, and the takeaway conveyor physically requires a few inches of final space above the floor.
Package attributes which impact the vertical space required include:
-
bag width - if you're a vertical bagging veteran this probably doesn't surprise you, but for many folks who work with the machines daily but haven't been involved in extensive project planning, bag width is the package factor with the biggest impact on machine height.
-
bag height - this is pretty obvious. The discharge chute needs to be long enough for you to have an entire bag hanging.
-
process speed - as noted above many of these food industry capital investments are predicated on increasing throughput speed and overall equipment effectiveness. As the primary goal it's not typically worth reverting to intermittent motion - although other improvements mitigate the compromise in some cases.
-
film thickness and structure - as noted above acute angles in forming often stress and break barrier structures like metalized layers. However this damage isn't necessarily obvious at the point of production on the machine. While fractures can often be identified with microscope inspection it's more common that the failure be identified during accelerated shelf-life testing of control samples, or even customer complaints about freshness and shelf-life. And this is an insidious problem for customers caught between machine suppliers who may compromise to meet ceiling height restrictions and film suppliers who provide the film!
We often encounter challenges in package attributes that actually stem from the range of flexibility specifications. These specifications may be designed for anticipated future requirements or for a small percentage of current production.
Let's take an example - high volume bag widths commonly range from 3-6" (80-140mm), but standard chassis sizes can accommodate up to 8". Engineering teams, who are accustomed to changing requirements from marketing and merchandising, naturally want to retain full flexibility for unknown future formats. While it's completely understandable, it's important to note that retaining that additional 2" of possible bag width could make a significant difference of several inches in the final machine height!
So, it's crucial to carefully consider these flexibility parameters when designing a vertical bagger to ensure it fits perfectly under existing constraints like a mezzanine. Don't get us wrong, we are all for maximum packaging machine flexibility, but it's not your most pressing issue.
3 Common "Tips" to Squeeze a Continuous Motion VFFS Under a Mezzanine
As you see above there are lots of reasons why the new, faster vertical bagger can't possibly fit under the existing ceiling.
But you must!
The good news is that there are some places we know from experience can resolve most of the conflict.
Compromise on bag size flexibility
Machines are designed for a wide range of materials, package formats and bag sizes. It's never easy to compromise on those options, and existing requirements such as bag width and film thickness structure often are set. But limiting operation to those known parameters allows for adjustment in various areas. While each may only capture 10-20mm, a series of those can add often add up to enough to fit the machine in.
Pop through the mezzanine
This isn't ideal, but it sure beats the alternative in many cases. Often the hopper can be fed from above the mezzanine and may even pop up through it. This isn't an option with a fixed ceiling obviously, and it limits floor space on the mezzanine and requires additional guarding and some process considerations. But when all else fails this is an expedient way to get the speed and efficiency increase that's needed.
Identify modules for compression
Rovema builds vertical baggers as a series of modules which are assembled vertically to perform functions as required. That provides flexibility to find opportunities within modules for compression. Because the functions are interrelated, and because the full range of capabilities interact in complex ways, this requires a detail review and agreement on what common flexibility can be compromised upon.
Other floor space considerations
Vertical bagging machines have inherently compact footprints - so there's typically no need to try to compress the length and width. However the common associated secondary packaging machines like cartoners, case packers and tray & lid style packing often do present floor space challenges when upgrading a line.
We'll tackle that in a future post, but there are a number of considerations - both in chassis design and integration which have been developed to fit within the constraints of more compact European factories. Rovema has considerable experience helping to shrink the size of lines while expanding the throughput and capability.
Need creative suggestions?
If you're like the majority of companies in the PackWorld survey and are trying to upgrade your vertical form/fill/seal operations within existing space limitations, let's talk. Our engineers nearly always find appropriate solutions by flexibly blending modular design with application requirements. Fill in the quick form below and we'll call to explore how to squeeze an upgraded vertical bagger under your existing ceiling/mezzanine: